Welding WPS Explained: Trick Elements and Conveniences for Your Welding Procedures
Opening the Power of Welding WPS: Approaches for Performance and Safety And Security in Manufacture
In the world of manufacture, Welding Treatment Specifications (WPS) stand as the foundation of welding operations, determining the essential steps for achieving both performance and security in the fabrication procedure. Recognizing the ins and outs of WPS is vital to utilizing its full potential, yet several companies have a hard time to unlock real power that exists within these papers (welding WPS). By delving into the strategies that maximize welding WPS, a globe of enhanced productivity and enhanced security awaits those ready to discover the nuances of this vital facet of construction

Significance of Welding WPS
The importance of Welding Treatment Specs (WPS) in the fabrication sector can not be overstated. WPS function as a crucial roadmap that describes the necessary actions to guarantee welds are executed constantly and correctly. By specifying vital parameters such as welding procedures, materials, joint designs, preheat temperature levels, interpass temperature levels, filler metals, and post-weld warm treatment needs, WPS offer a standardized method to welding that improves efficiency, high quality, and safety in fabrication processes.
Adherence to WPS helps in accomplishing uniformity in weld top quality, lowering the likelihood of problems or structural failures. This standardization additionally helps with conformity with industry guidelines and codes, ensuring that produced frameworks meet the required safety standards. Moreover, WPS paperwork makes it possible for welders to replicate effective welding treatments, leading to constant outcomes throughout various jobs.
Basically, the careful advancement and rigorous adherence to Welding Treatment Requirements are vital for promoting the stability of welded structures, securing versus possible threats, and promoting the credibility of fabrication companies for providing top notch services and products.
Key Elements of Welding WPS

Enhancing Effectiveness With WPS
When enhancing welding operations, leveraging the vital components detailed in Welding Procedure Specifications (WPS) comes to be necessary for enhancing procedures and making best use of efficiency. One method to improve effectiveness with WPS is by thoroughly picking the proper welding parameters.
Additionally, correct training and certification of welders in understanding and implementing WPS can even more boost performance. Guaranteeing that all staff member are well-versed in translating and executing the WPS properly can reduce mistakes and rework, saving both time and sources. Routinely reviewing and upgrading the WPS to integrate any kind of lessons discovered or technological innovations can likewise add to efficiency enhancements in welding procedures. By accepting the standards set forth in the WPS and constantly looking for ways to enhance procedures, fabricators can accomplish greater efficiency degrees and premium outcome.
Ensuring Safety in Fabrication
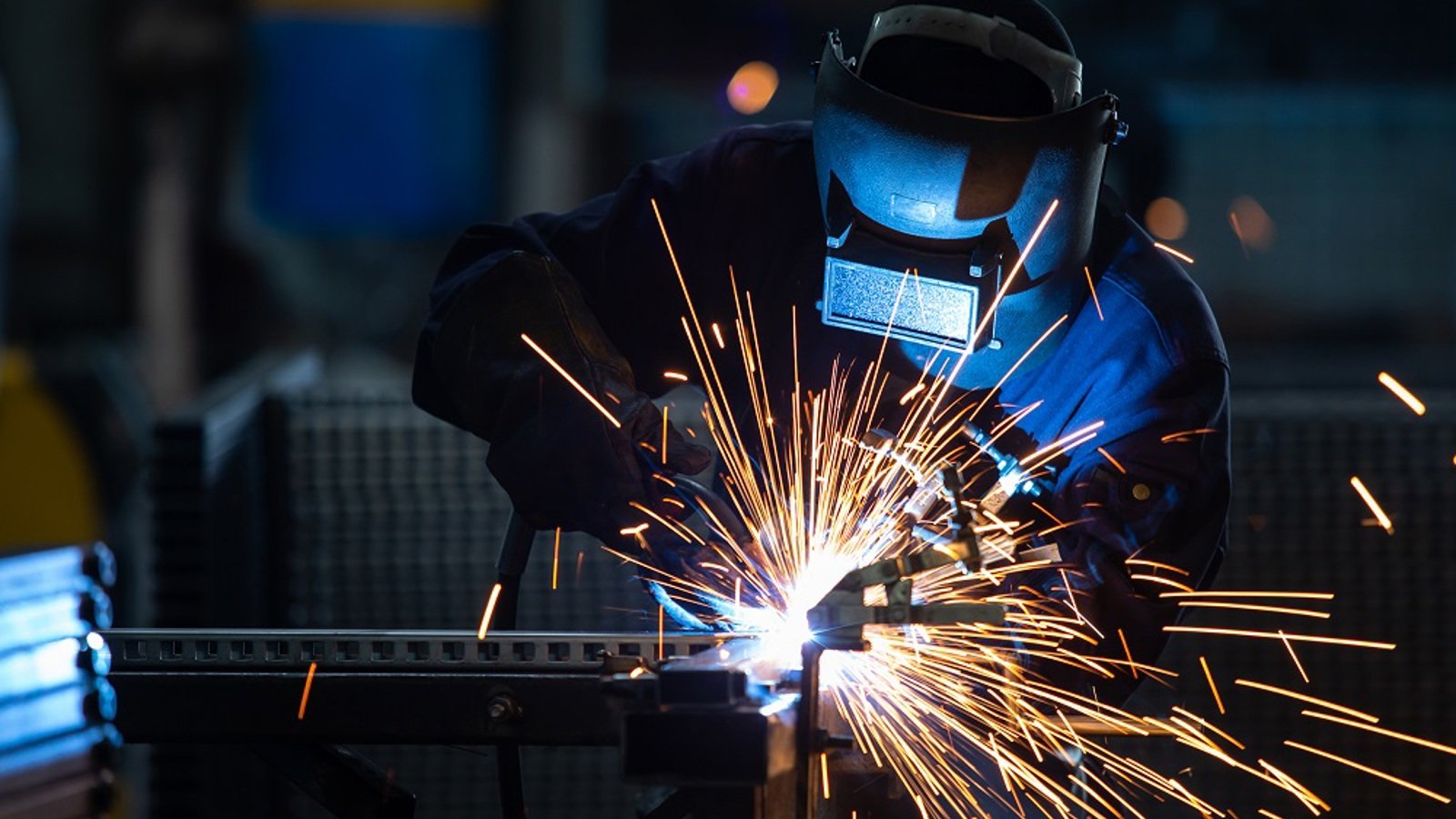
Ensuring security in fabrication entails a diverse strategy that includes various facets of the welding process. Welders have to be geared up with ideal gear such as headgears, gloves, and protective garments to reduce dangers associated with welding tasks.
Furthermore, adherence to appropriate air flow and fume extraction useful reference systems is vital in keeping a healthy job environment. Welding fumes contain unsafe substances that, if inhaled, can pose serious health risks. Carrying out effective ventilation procedures aids to minimize direct exposure to these hazardous fumes, advertising respiratory health and wellness amongst workers.
Regular tools upkeep and inspections are additionally important for making sure safety and security in fabrication. Malfunctioning equipment can lead to injuries and mishaps, emphasizing the relevance of routine checks and timely repair services. By focusing on safety and security measures and promoting a culture of understanding, manufacture centers can develop a efficient click this site and protected job environment for their workers.
Carrying Out WPS Ideal Practices
To improve functional effectiveness and make certain high quality end results in construction procedures, incorporating Welding Treatment Specification (WPS) finest techniques is critical. Picking the suitable welding procedure, filler material, and preheat temperature defined in the WPS is essential for attaining the desired weld high quality. Making certain that qualified welders with the needed qualifications carry out the welding treatments according to the WPS standards is important for uniformity and integrity.
Conclusion
In final thought, welding WPS plays a crucial function in making sure performance and safety in construction procedures. By concentrating on crucial elements, improving performance, and implementing best methods, business can maximize their welding procedures. It is vital to prioritize security procedures to avoid accidents and guarantee a smooth production process. By following these strategies, organizations can unlock the full potential of welding WPS in their construction operations.
In the world of manufacture, Welding Treatment Requirements (WPS) stand as the foundation of welding procedures, dictating the necessary steps for achieving both efficiency and security in the fabrication process. By specifying crucial criteria such as welding procedures, products, joint styles, preheat temperatures, interpass temperatures, filler steels, and post-weld warmth treatment requirements, WPS offer a standardized approach to welding that visit this site enhances efficiency, quality, and safety and security in manufacture procedures.

When maximizing welding operations, leveraging the crucial aspects laid out in Welding Procedure Specs (WPS) comes to be important for enhancing procedures and making the most of efficiency. (welding WPS)